First time to business trip!
- martin.tsou
- Dec 17, 2019
- 3 min read
Updated: Dec 18, 2019
June 14th, 2019, started my first business trip, Kunshan, China.

At this time, I had just been in the Mitac ID team for half a year, our manager, Matthieu helped me immediately to get a chance to visit Mitac assembly factory.
To let me deeply understand the knowledge of [Production Line] and [Tooling] and the product manufacturing process. For me who is a fresh graduate, I have learned a lot and let me eye-opener.
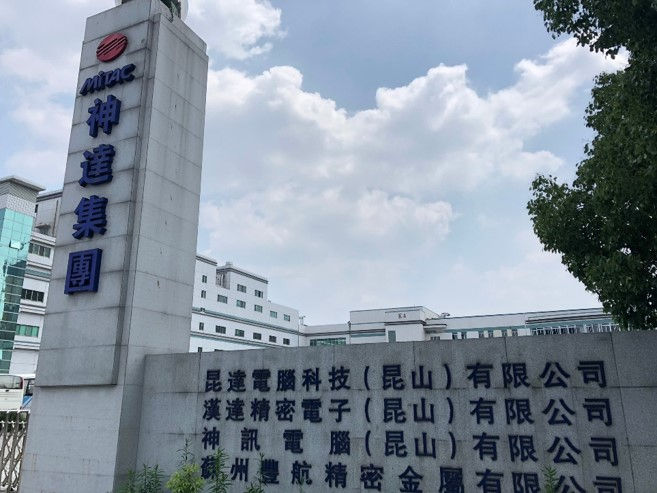
【Production Line】
In the assembly factory, I saw that the product needs to go through dozens of procedures to produce from scratch. Obviously, from product assembly, parts manufacturing to packaging are very complicated.
In the assembly factory, I saw that the product needs to go through dozens of procedures to produce from scratch. Obviously, from product assembly, parts manufacturing to packaging are very complicated. Ex. PCBA manufacturing, components welding, X-ray checking, second time welding, ICT, components assembly, reliability test and shipment, are all done by many methods, technologies and complete production line planning.
By the way, I am very happy to be an operator at the production line.
During the product assembly process, I was exposed many auxiliary materials with different specifications and types, such as sponges, heat sinks, mylar, iron covers and tapes.
Due to the different sizes of the auxiliary materials, the operator needs to focus on attaching the auxiliary materials to the correct positions. Some actions seems simple, but operate very difficult actually, and it is easy to lose or damage the auxiliary materials.
In the two-days production line experience, I fully understood the operator's hard work, and knew that too much auxiliary material would affect the product yield and the cost efficiency.
【Tooling Vendor】
On the third day, I go to the tooling manufacturer (vendor) with the IE (production management department) to see the samples, and have the opportunity to observe the production process of the tooling, and understand the production, type, and product finish manufacturing process.

Once at the door of the manufacturer's company, a row of fixtures lay on the ground. It was so cool! Can't wait to understand the different fixtures more clearly.
There are many different types of fixtures in the factory, such as for testing, assembly, and cutting applications. These fixtures are used to assist operators, increase assembly accuracy, and make the work process smoother and faster.
In the laser room, the laser-engraved steel plate is used for soldering PCBA.
This is a part that is rarely encountered and learned in general design experience. Although it is not related to the design, we can know the precision of the fixture.
【 Fun and value of manufacturing discover this time ! 】
After a week's visit to the production line, operator experience, and inspection of the fixture factory, it was found that the product output, from design and development to shipment, requires many people and methods to work together. Each part of the production process is like the small screws on the machine, no one is indispensable.
In the production line experience, I realized that there are many specifications and quantities of auxiliary materials that can be reduced in the structure and mechanical design in the product development stage. It will more efficient in terms of time and manpower.
This business trip is a very special and rare experience. Observing the entire product manufacturing process is a rare learning resource and opportunity for many designers and other companies.
Through this learning experience, our ID product design can be more predictive of product manufacturing, and integrate with the rear end, so that design can be more complete.
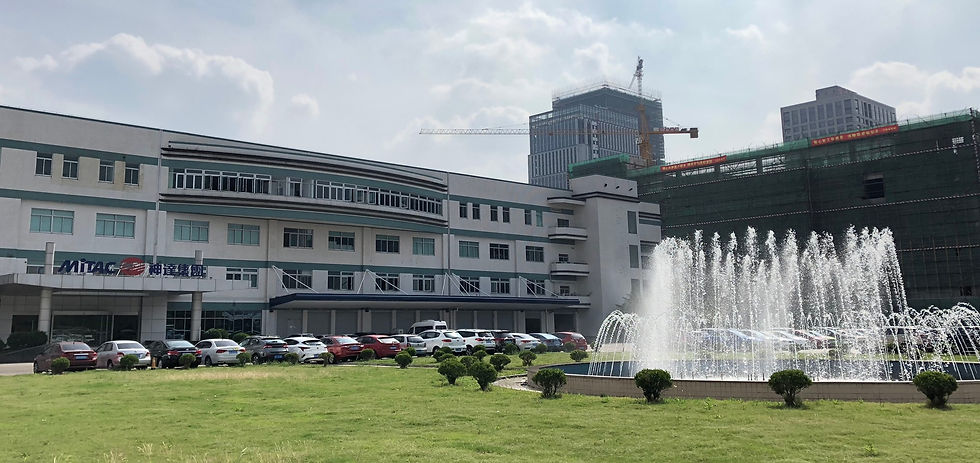
Comments